The Manufacture of Cleaning Materials: A Comprehensive Overview
The manufacture of cleaning materials is a complex and multifaceted industry that plays a crucial role in maintaining hygiene and sanitation in homes, workplaces, and public spaces. From household cleaners to industrial-grade detergents, the process involves various stages, from raw material sourcing to the final packaging of the product. This article explores the key aspects of cleaning material manufacturing, including the types of cleaning agents, production processes, quality control, and environmental considerations.
Types of Cleaning Materials
Cleaning materials can be broadly classified into several categories based on their chemical composition and intended use. The main types include:
1.Detergents: These are surfactants that lower the surface tension of water, making it easier to remove dirt and grease. Detergents are commonly used in laundry and dishwashing applications.
2.Disinfectants: These are chemical agents designed to kill or inactivate harmful microorganisms. Disinfectants are used in healthcare settings, food processing plants, and household cleaning products.
3.Abrasives :These materials are used to remove stubborn stains and grime through mechanical action. They are often found in products like scouring powders and scrubbing pads.
4. Solvents: Solvents dissolve oils and grease, making them effective in cleaning tasks such as degreasing machinery or removing stains from fabrics.
5.Bleaching Agents: These chemicals, such as chlorine or oxygen-based bleaches, are used to whiten fabrics, disinfect surfaces, and remove stains.
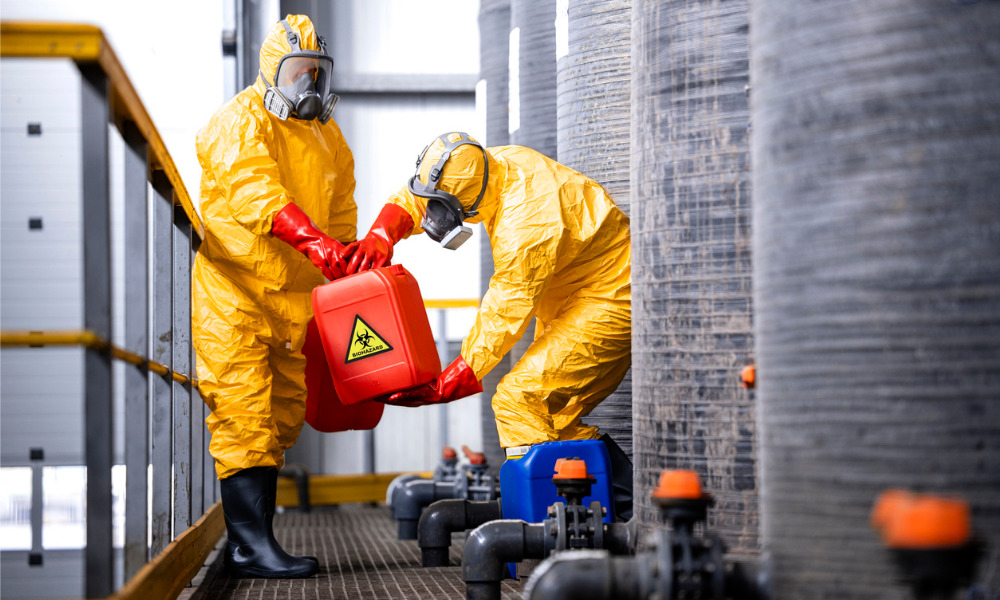
Production Processes
The manufacturing of cleaning materials involves several key processes, each tailored to the type of product being produced:
1.Raw Material Sourcing: The production process begins with the sourcing of raw materials, which include surfactants, solvents, fragrances, dyes, and other chemical agents. These materials are typically sourced from chemical suppliers and must meet stringent quality standards.
2.Formulation: In this stage, the raw materials are blended in precise proportions to create the desired cleaning product. The formulation process is critical, as it determines the effectiveness, safety, and stability of the final product. Advanced computer software is often used to model and optimize formulations.
3.Mixing and Compounding: The formulated ingredients are mixed in large industrial mixers or reactors. This process ensures that the components are thoroughly blended, resulting in a homogeneous mixture. The mixing process may involve heating or cooling to achieve the desired consistency and chemical reactions.
4.Quality Control: Throughout the manufacturing process, rigorous quality control measures are implemented to ensure that the product meets all regulatory and safety standards. This includes testing for pH levels, viscosity, stability, and microbial contamination. Quality control laboratories often perform these tests using advanced analytical equipment.
5.Packaging: Once the product has passed quality control checks, it is transferred to the packaging line. Packaging materials such as bottles, cans, and pouches are filled with the cleaning product, labeled, and sealed. The packaging process is highly automated, with machines designed to fill, cap, and label products at high speeds.
6. Distribution: After packaging, the products are distributed to retailers, wholesalers, and direct consumers. Effective distribution channels are essential to ensure that the products reach the market in a timely manner.
Environmental and Safety Considerations
The manufacture of cleaning materials raises important environmental and safety concerns. Manufacturers are increasingly adopting sustainable practices to minimize the environmental impact of their operations. This includes the use of biodegradable ingredients, reducing waste through recycling and reusing packaging materials, and implementing energy-efficient production processes.
Safety is another critical aspect of the cleaning material industry. Manufacturers must comply with regulations governing the safe handling, storage, and disposal of chemicals. Workers involved in the production process must be trained in proper safety procedures and provided with protective equipment to prevent exposure to hazardous substances.
Innovation and Trends
The cleaning material industry is constantly evolving, driven by consumer demand for more effective, convenient, and environmentally friendly products. Recent trends include:
1.Green Cleaning Products: There is a growing demand for cleaning products made from natural, non-toxic ingredients. Manufacturers are responding by developing eco-friendly products that are safe for both humans and the environment.
2.Concentrated Formulations:Concentrated cleaning products are becoming increasingly popular due to their reduced packaging and transportation costs. Consumers can dilute these products at home, which also helps reduce the environmental footprint.
3.Smart Cleaning Devices: The integration of cleaning materials with smart technology is another emerging trend. For example, robotic vacuum cleaners that automatically dispense cleaning agents are gaining popularity in the market.
Conclusion
The manufacture of cleaning materials is a dynamic industry that requires a careful balance of science, technology, and environmental stewardship. As consumer preferences shift towards more sustainable and innovative products, manufacturers must continue to adapt and evolve their processes. With advancements in technology and a focus on sustainability, the future of the cleaning material industry looks promising.